Most common construction planning mistakes
17 March 2021
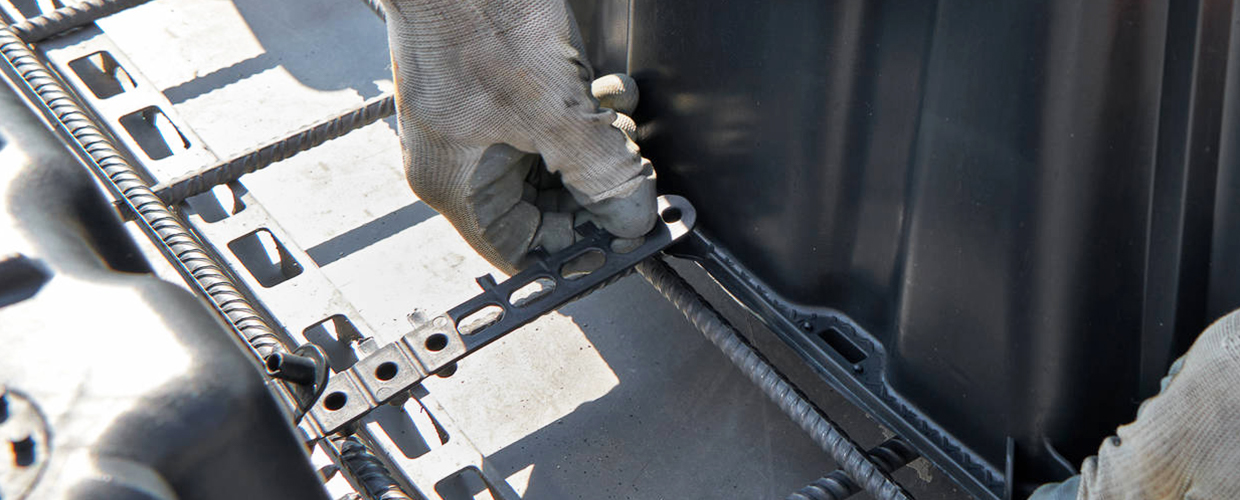
Based on our experience, there are mistakes that are fully avoidable and yet persistently made in construction planning. You could escape many of them in the future, in order to increase the sustainability and profitability for both builders and users of your projects.
Non-ventilated foundations
Rising damp and Radon gas can build up under the foundations if they are not properly ventilated. Geoplast foundations products are designed to form crawl spaces that help the elimination of harmful vapors.
Heavy formwork
Using formwork that is heavy and non-modular demands a huge amount of storage space, machinery, and assembly time. Geoplast formworks are made of modular plastic elements that can be assembled quickly and easily by a single worker.
Non-reusable formwork
Installing non-reusable formwork increases the amount of waste and the cost of transport to landfills. Compared to 15 to 20 uses of traditional plywood, Geoplast plastic formwork can be reused a 100+ times, which significantly reduces the final building costs.
Full slabs
By building full concrete slabs more material is used, which implies more bearing walls and columns, and a lowered seismic resilience of the building. Geoplast voided slab formworks offer various benefits, among other a 30% lower seismic mass and a reduction in construction costs.
No space for MEP
The planning of MEP systems is considered a separate job from planning the structural elements. This results in higher construction costs, lowered seismic resilience, and an uninspectable MEP space. Geoplast foundations and slab formworks are designed to create technical compartments within the concrete itself, with less need for masking the infrastructure.
Non-sustainable isolation
Green roofs and walls are usually not accounted for when planning thermal and sound isolation of the building. Geoplast offers sustainable green solutions that can reduce energy costs by up to 35%.
Paved parking lots
Planning traditional paved parking decreases flood resilience in urban areas. Green parking solutions greatly improve rainwater management and can be installed quickly on new or existing grass surfaces.
Using gravel for drainage
Gravel is not inspectable and using it as a drainage layer under the foundations or paved surfaces may cause later maintenance difficulties. Geoplast water products are able to retain 3 times more water than gravel, while remaining fully inspectable and efficient in increasing drained areas.
Non-sustainability
Using too much concrete and old cement formulas endangers the environment. Geoplast foundations and slab products can help save up to 20% of concrete, thus reducing building time, machinery use, and CO2 emissions.
We hope you found this list informative and useful for planning your next project.